High-speed inner diameter processing optical system
Conventional laser hardening is performed on steel surfaces by positioning the laser beam with a robot arm, galvanometer, or by moving the workpiece to adjust the hardening position. In contrast to induction hardening and carburizing hardening, laser hardening can be applied to only partially required areas. Therefore, it saves energy and meets the development targets of the SDGs, whereas other hardening methods require large amounts of energy.
However, while laser hardening of steel surfaces has become common, hardening of inner diameters (e.g., bearings and irregularly shaped sliding parts), even in the case of induction hardening, requires highly skilled techniques due to the complex coil structure. In addition, it was required to re-build for each size of inner diameter.
The inner diameter processing optical system developed by WIRED (from φ50mm) eliminates these troublesome processes and enables easy hardening at the desired location. Furthermore, the optics can handle high repetition rates of picosecond and femtosecond lasers, which are called ultrashort pulsed lasers, and thus have the ability to enable laser honing processing. By applying the optical systems that we offer, we can provide you with inner-diameter hardening processing machines and laser honing technology.
Ⅰ.Laser hardening results
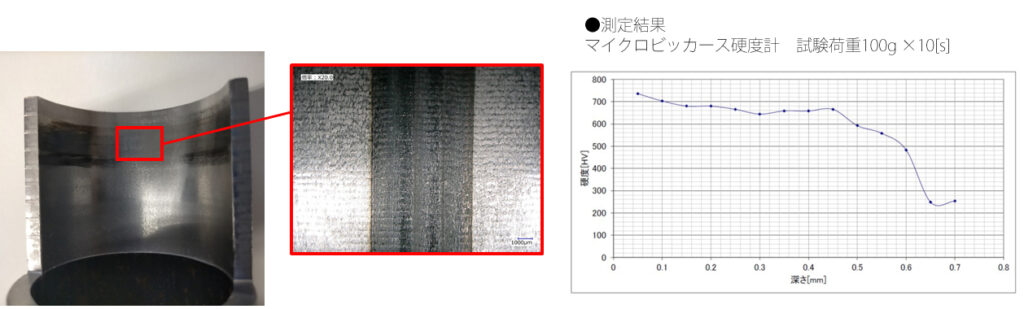
Ⅱ.Dimpling example
In addition to hardening, lubrication by oil film is promoted by adding dimples and grooves to the inner surface.

Ⅲ.Other processing examples
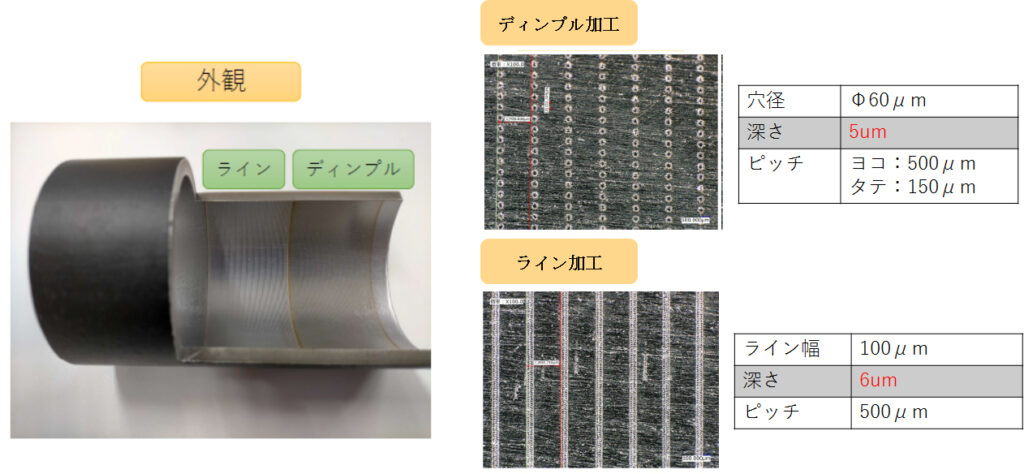
Ⅳ.Experimental Equipment
Experimental devices that apply optics for inner surface processing are located in the main office. The optical system has a maximum rotation capacity of 7,000 rpm but can be further developed to meet your objectives.
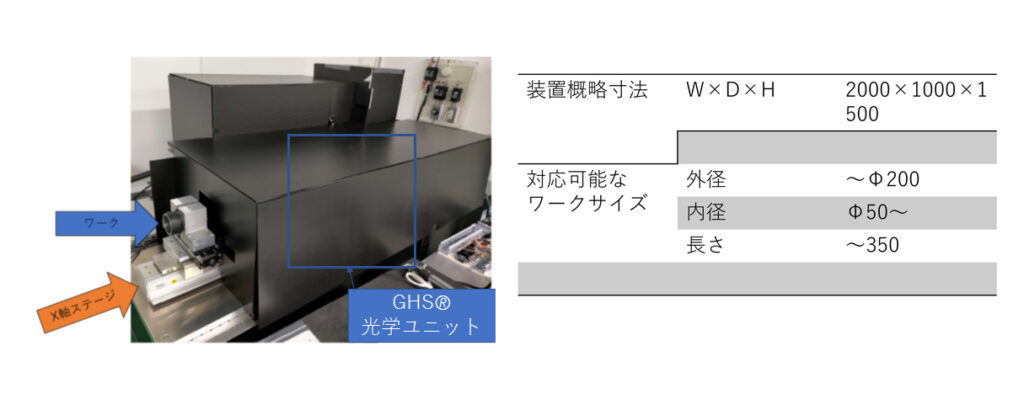