High capacity lithium-ion batteries! Laser drilling of a whole electrode
High capacity lithium-ion batteries! Laser drilling of a whole electrode.
Easily achieve “pre-doping
Nikkei Electronics October 2018
Wired Co., Ltd., a venture company that specializes in microfabrication technology, has developed a technology that continuously opens a large number of fine holes with a laser into the electrode material of lithium (Li) ion 2 batteries (Figure 1).
By using the drilling electrode material, “pre-doped” of Li ions, which is essential for high capacity of the next-generation Li ion 2 battery can be easily realized.
Figure 1: Laser processing of the electrode scavening
An electrode coated with Si anode on stainless steel was drilled by laser processing. When a light is shone on the back of the electrode, you can see that light is being dropped into it.
Breaking the bottleneck of high capacity
Pre-doping is a technology to solve the problem of the decrease in the amount of Li ions involved in charging and discharging as the battery is used.
If this problem is not solved, even if the electrode materials are combined with high-capacity electrode materials, it will be impossible to obtain a capacity that matches the potential of the battery.
The decrease in the amount of Li ions involved in charging and discharging in Li-ion batteries is due to the formation of compounds with Li on the electrodes during the initial charging process.
The Li incorporated into the compound does not ionize when charged and discharged, and its capacity decreases. In other words, the irreversible capacity increases.
For this pre-doping, a Li foil is placed in the cell beforehand to provide a source of Li ions in anticipation of a decrease in Li ions.
The Li foil is short-circuited to the negative electrode outside the cell to allow the Li ions to move inside the cell (Fig. 2).
By realizing the pre-doping, there is a possibility that it is possible to expand the use of electrode materials that have not been practical while high capacity so far.
These include materials with large irreversible capacity and high capacity cathode materials that are not Li compounds.
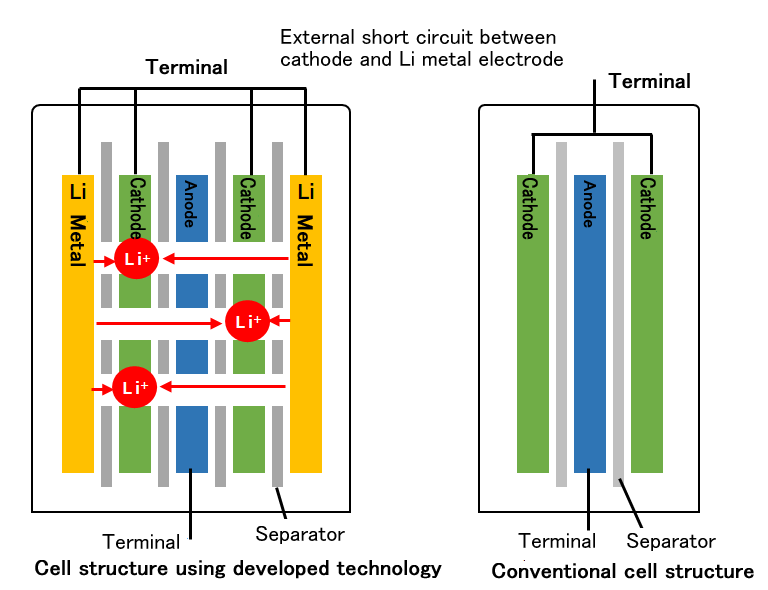
Figure 2: Pre-doped cell structure with laser-machined electrodes
By pre-doping, the insufficient Li can be supplied into the cell, and high capacity can be achieved.
Processing into Si negative electrode stainless steel aggregate
Wired Co.,Ltd.,first aims to apply to si (silicon) negative electrode, which is expected to spread as a high-capacity negative electrode material.
The si negative electrode has a theoretical capacity of 4200mAh / g, although it is more than 10 times higher than the existing graphite negative electrode, the initial charging efficiency is lowered to about 80% if not predoped.
Moreover, it is easy to use the processing technology in which the company excels for Si negative electrode.
Because of the large change in expansion and contraction during charging and discharging, the electrode current collectors are not made of Cu (copper) foil, but rather high-strength The reason for this is that the adoption of a rigid stainless steel is being considered.
The stainless steel, it is difficult to open a fine hole for pre-doping, there is a possibility of internal short circuit due to burrs even even drilling.
The company’s processing technology made it possible to make holes in the electrodes after coating the Si anode with stainless steel. (Figure 3).
The reason for this is that it is possible to drill through holes in a composite consisting of multiple materials at once. Therefore, the drilling process only needs to be added to the conventional electrode manufacturing process.
Using the company’s processing technology, the si negative electrode can be drilled at any aperture rate to the electrode after the negative electrode is applied to stainless steel (Figure 3).The reason is that the through hole can be opened at a dash for the composite which piled up a plurality of materials.Therefore it is only to add a drilling step to the conventional electrode manufacturing process.
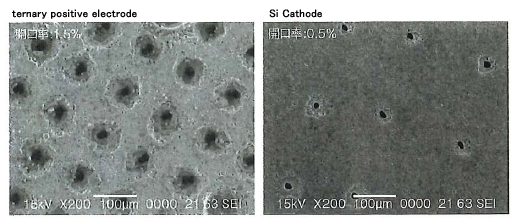
Figure 3: Laser-processed electrodes at a constant aperture ratio
The left is drilled with an opening ratio of 1.5 to the ternic positive electrode material, and the right is drilled with 0.5% of the opening scattered on the Si negative electrode material.
The company’s drilling technology is capable of drilling 40 to 300,000 holes per second by irradiating a laser beam.
It is faster than existing laser processing techniques. The diameter of the holes ranges from 3 µm to 20 µm, making them smaller than those made by existing laser processes.
No burrs can be created, according to the company. It is also faster and smaller in diameter than punch presses and etching.
Prototype of 1Ah-class laminated cell
With the help of Yamagata University, which is developing batteries for electric vehicles, the company prototyped and tested a 1Ah-class laminated cell. Ternary cathode material made of nickel (Ni), manganese (Mn), and cobalt (Co) and an anode material made of silicon (Si) were through-hole-machined by laser, and Li foils were placed on both sides of the stacked electrodes and the anode and Li foils were short-circuited externally (Figure 4). Succeeded in pre-doping Li ions to the negative electrode, the initial charge-discharge efficiency was increased to 93%.The series of technologies utilizes some of the results of the new Energy and Industrial Technology Development Organization(NEDO) grant project.
Figure 4: Charging and discharging efficiency is now 93% due to the effect of pre-doping.
A 1Ah-class battery cell using the Si negative electrode was prototyped (left).Li metal station and the negative electrode was realized predoped by external short circuit.The test after pre-doping achieved the initial charge-discharge efficiency of 93° (right).
WIRED Co., Ltd. aims to reduce the continuous processing time and cost of laser processing in the future.
We are also considering applications other than pre-doping. For example, it is thought that the cell output can be increased by forming a recess on the electrode surface by laser processing.
Click here for Nikkei XTECH articles
Lithium-ion battery related information
High-speed laser punching technology was introduced in NIKKAN KOGYO NEWSPAPERS.
Laser Processing Services
Our laser processing technology enables high-speed, non-contact processing of fine holes with significantly smaller diameters and fewer burrs compared to other drilling methods such as punch presses and etching.
Laser Processing Machine Manufacturing
We manufacture and sell roll-to-roll laser drilling machines equipped with our original optical system GHS (Grand Helical Scan).
Laser Technical Data
Introduces laser processing technology, treatises, and laser processing examples.